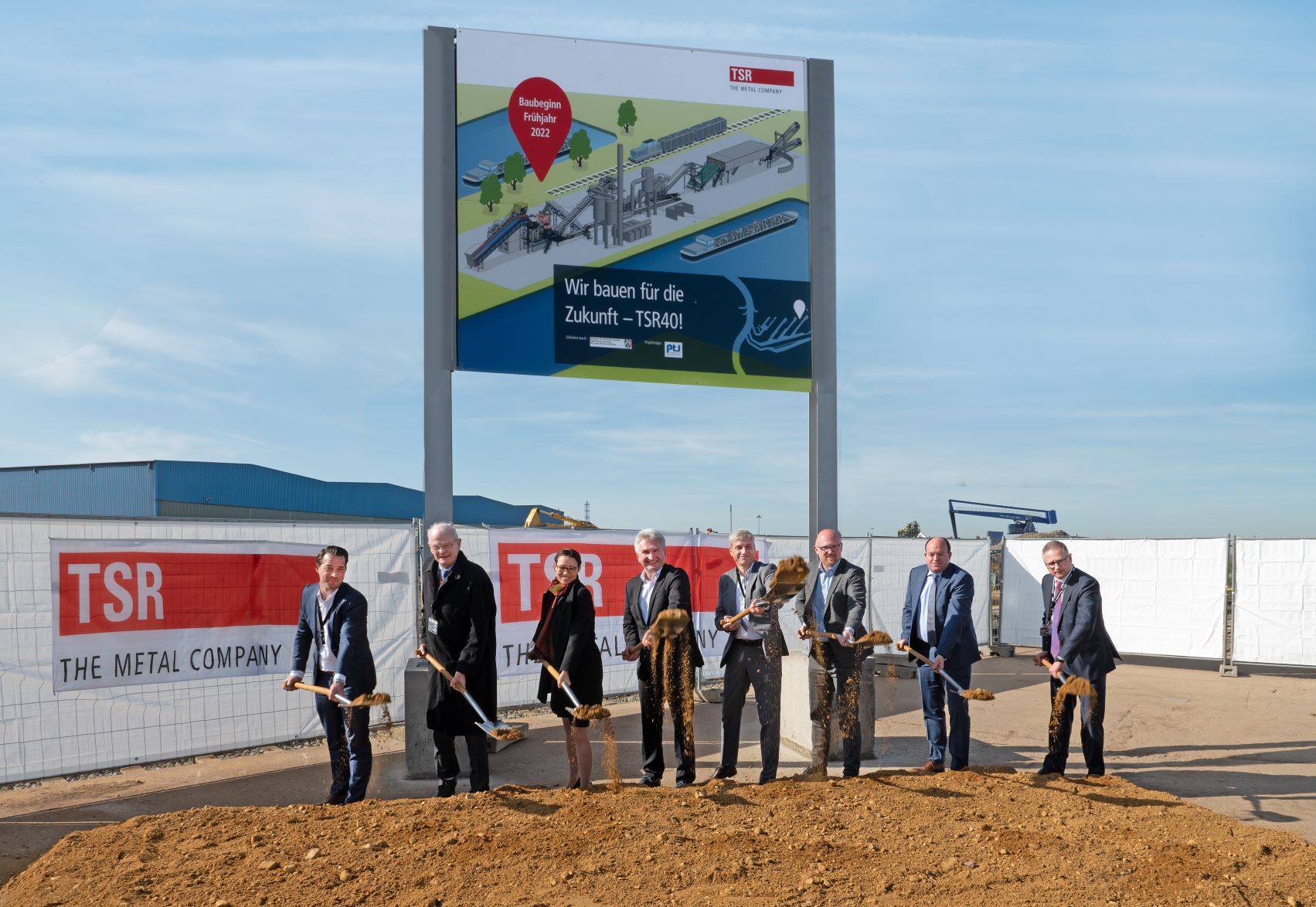
At Thyssenkrupp Steel’s recycling location in the Duisburg inland port, on the so-called Schrottinsel (scrap island) in Duisburg, the groundbreaking ceremony for the construction of a scrap processing plant by TSR Recycling took place today. The processing plant is part of the Reders project (reduced CO2-emissions through increased recycling quota in the steelmaking process) funded by the state of North Rhine-Westphalia in the amount of € 6.4 million, which marks another steps towards a reduction of CO2 emissions in the steel industry through the establishment of a recycling center for steel scrap. The project partners in this initiative of the circular economy aimed at conserving resources are TSR and Thyssenkrupp Steel as well as Hüttenwerke Krupp Mannesmann and VDEh Betriebsforschungsinstitut. Through the use of innovative processes, the processing plant is to produce a high-quality recycled raw material (TSR40) intended for use in the Duisburg blast furnaces of Thyssenkrupp Steel.
Steel scrap is an indispensable raw material for the circular economy
Recycling to recover valuable materials is an essential factor in the supply of raw materials for the primary industry. Especially steel scrap more than 95 % of which is recycled and reused, is of outstanding importance for the production of crude steel. Particularly in the North Rhine-Wesphalia, an important business location, metal recycling for the steel industry is a lever both for conserving resources and for reducing CO2 emissions. North Rhine-Wesphalia’s Economics Minister Prof. Dr. Andreas Pinkwart: “Transformation towards a future-oriented and climate-friendly industry is a task we must tackle with joined forces. To achieve this, we need to bring together the strengths of individual sectors and tap into their shared potential. The close collaboration of the North Rhine-Westphalian steel and recycling sectors in the Reders project shows how this can be successfully done at the Duisburg location with its rich and long tradition. I firmly believe that this project will lead the way for the entire industry“.
Special processing technology provides recycled base material for steel production
The use of steel scrap in the blast furnaces of Thyssenkrupp requires special material properties of the recycled product. Automated charging of the blast furnace requires a material that is as homogeneous as possible in terms of size and contour, so that blockages during material transport can be ruled out. Moreover, there are exact requirements regarding analytical impurities as unwanted tramp elements cannot be separated in the subsequent steelmaking process. Both requirements are met in the new processing plant, which is equipped with a special shredder and separation technology with subsequent online analysis and documentation software. Bernd Fleschenberg, TSR’s Managing Director: “Apart from the positive effects for environmental protection and resource conservation, the construction of the new plant and the novel product are also representative of sustainable and reliable raw material supply in Germany and Europe. TSR40 enables us to cover large part of future raw material requirements of the industry. Particulary in view of interrupted supply chains, our plant at the Duisburg location is a lighthouse project that can serve as a model for other material flows”.
Measurable CO2 reduction through certified recycling approach
The use of this specially processed scrap product allows at the same time to reduce CO2 emissions since an increased quantity of metallic iron in the form of recycled raw materials leads to a reduced consumption of iron ore and carbon carriers (coke, coal) to produce an identical amount of steel. Besides the long-term transformation of production processes to climate-neutral steelmaking, a reduction in CO2 emissions can thus be achieved in the very short term by increasing the recycling quota. About 1 tonne of CO2 per tonne of recycled material can be avoided in the blast furnace. Thyssenkrupp Steel’s CTO Dr. Arnd Köfler: “This project enables us to make rapid progress in the reduction of CO2 emissions. Aside from the long-term transformation of our plant and equipment to hydrogen-based direct reduction, we are already doing everything possible to avoid CO2 in the conventional blast furnace process as well. The use of scrap-based recyled material in the blast furnace is an important step in this direction which also benefits our customers“. For the use of recycled products in the blast furnace allows to achieve and report a reduction of the CO2 intensity from 2.1 of 0.75 tonnes in balance sheet terms. This fact has been certified by TÜV Süd in accordance with the Veristeel process and forms the basis for the Thyssenkrupp Steel‘s CO2-reduced product Bluemint Recycled. In the future, TSR’s processing plant will support the production of the Bluemint steel range by providing a high-quality recycled product. Once the plant is completed, up to 260,000 tonnes of Bluemint Recycled can be produced per year on this basis.