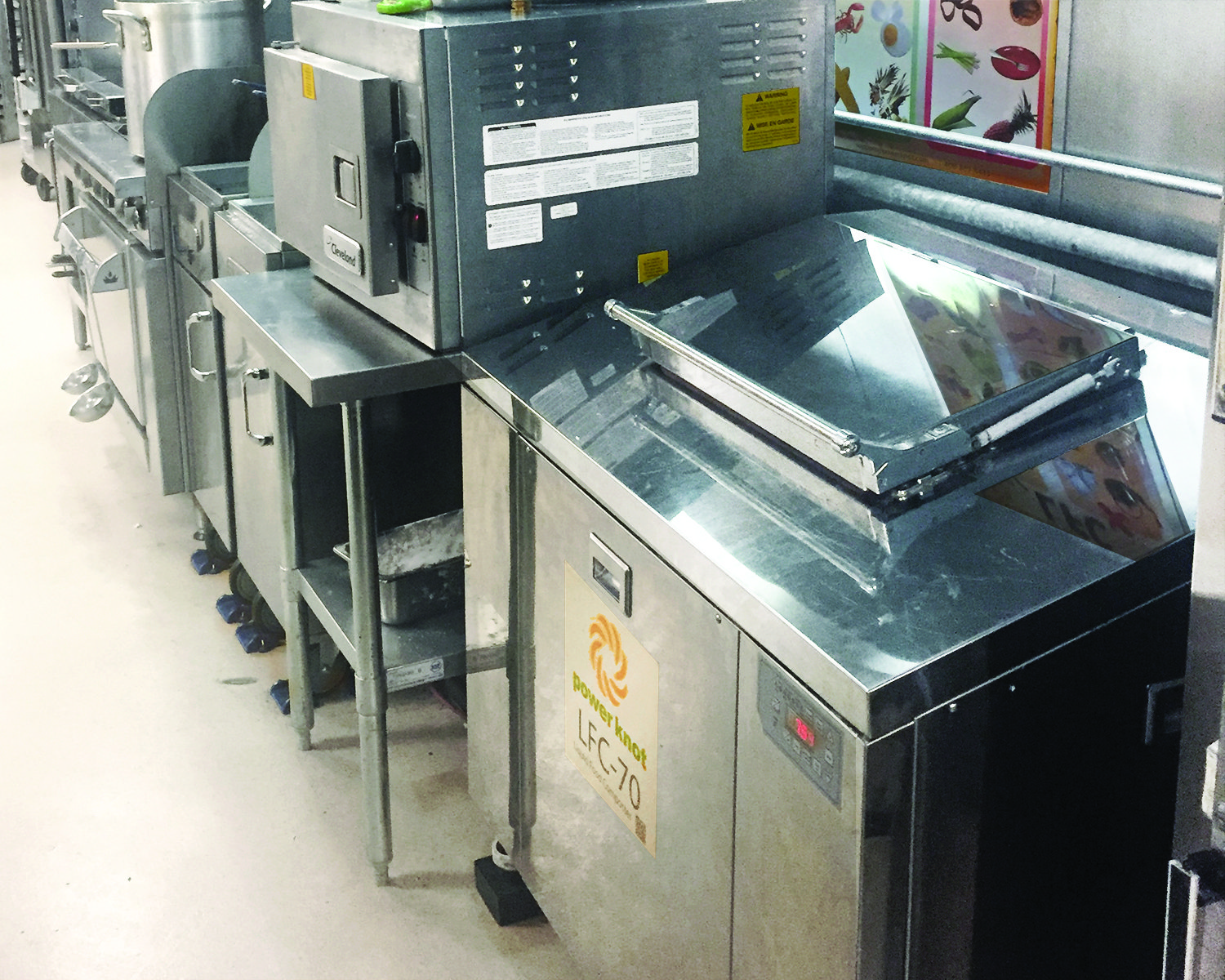
Manufactured by Power Knot LLC of San Jose, CA, the cafeteriaâs LFC-70 biodigester uses a mix of natural microbes and enzymes, along with infusions of hot and cold water and oxygen, to aerobically convert biodegradable food waste into grey water that drains into municipal waste lines.
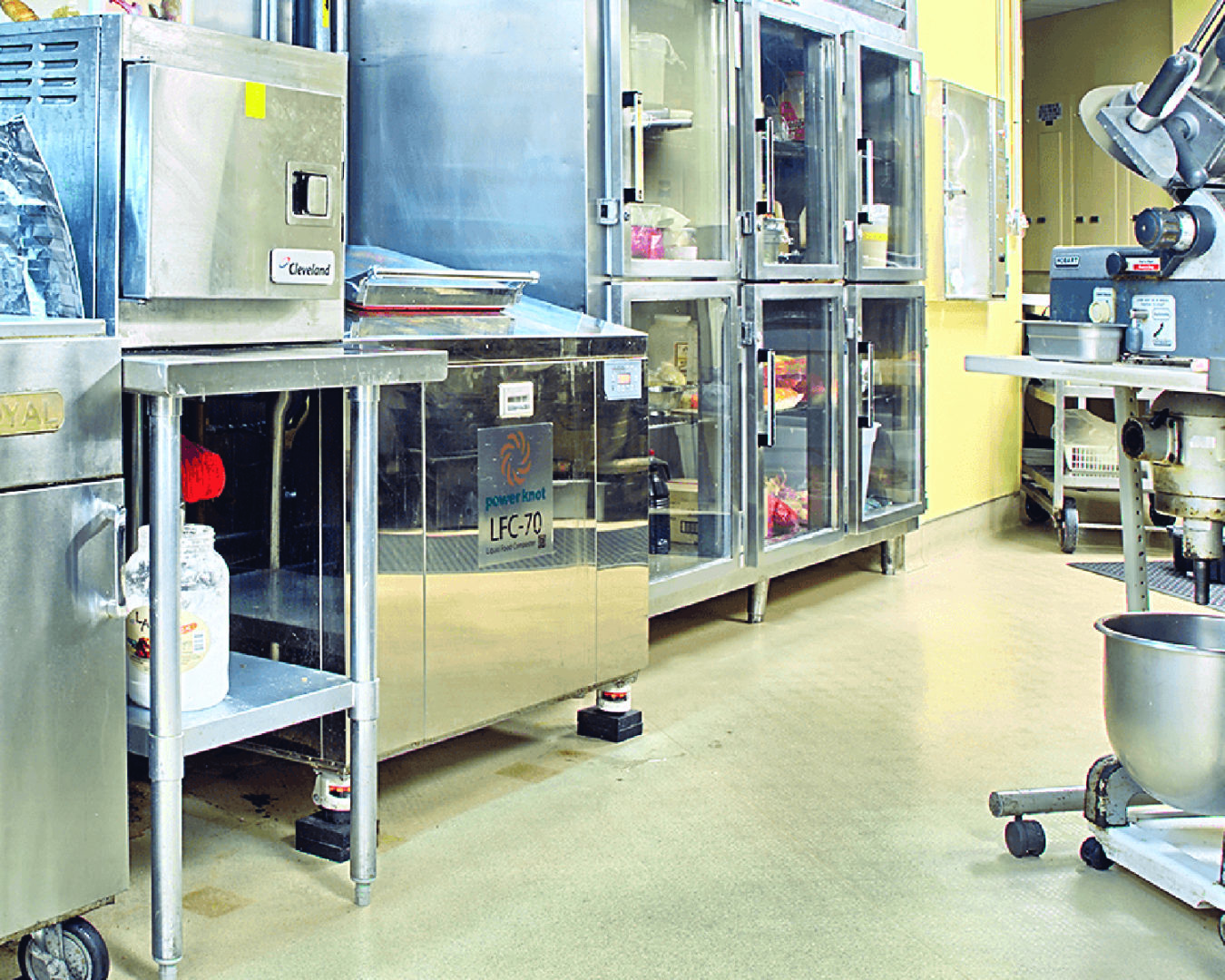
The facility serves breakfast and lunch to approximately 150 employees, generating about 50 kg of food waste per day. Robert Curtis, environmental, health, safety, and security services specialist, says the biodigester can process up to 125 kg of waste every 24 hours.
Employees separate packaging from the food, and load waste through a hinged lid on top of the stainless steel enclosure.
âThe machine doesnât cycle, so we can keep adding waste,â Curtis says. âSome employees wanted to accumulate food scraps, but itâs better to keep adding waste as itâs generated.â
Curtis says the process is relatively odour free. âIt smells faintly like cantaloupes.â As a result, the unit does not attract pests and can be installed in the kitchen rather than in a special area.
In addition to reducing disposal costs, diverting roughly 13 tonnes of food waste from landfills reduces CO2 emissions by about 46 tonnes per year.
Information on drum temperature, door openings, water volume, water temperature, CO2 emissions avoided, service reminders, and weight of the food waste digested by hour, day, week, month and year can be accessed on the unitâs touch screen or a smart device, laptop or computer via the cloud.