
If it is purely about volume reduction, for example for easier transport, this can be achieved with conventionally designed shafts. Some applications, however, require specific particle sizes for their processes. Plants that recover energy from waste wood, for example, are usually designed with a standardised particle size in mind. Oversized particles in the material stream can block the conveyors or safety systems such as rotary valves. In addition, too many fines negatively affect combustion and very small particles might lead to lumps jamming the facility. Therefore, if the required size is not obtained in the first shredding step, the material must be treated further. The crux of the matter is that additional processing is costly, reduces the recycler’s profit margins and, in the worst case, leads to customer complaints. To avoid these problems, Lindner’s patented SF synchronous fine cutting system is specifically designed based on the following two simple principles.
Scissors and Archimedes’ Screw
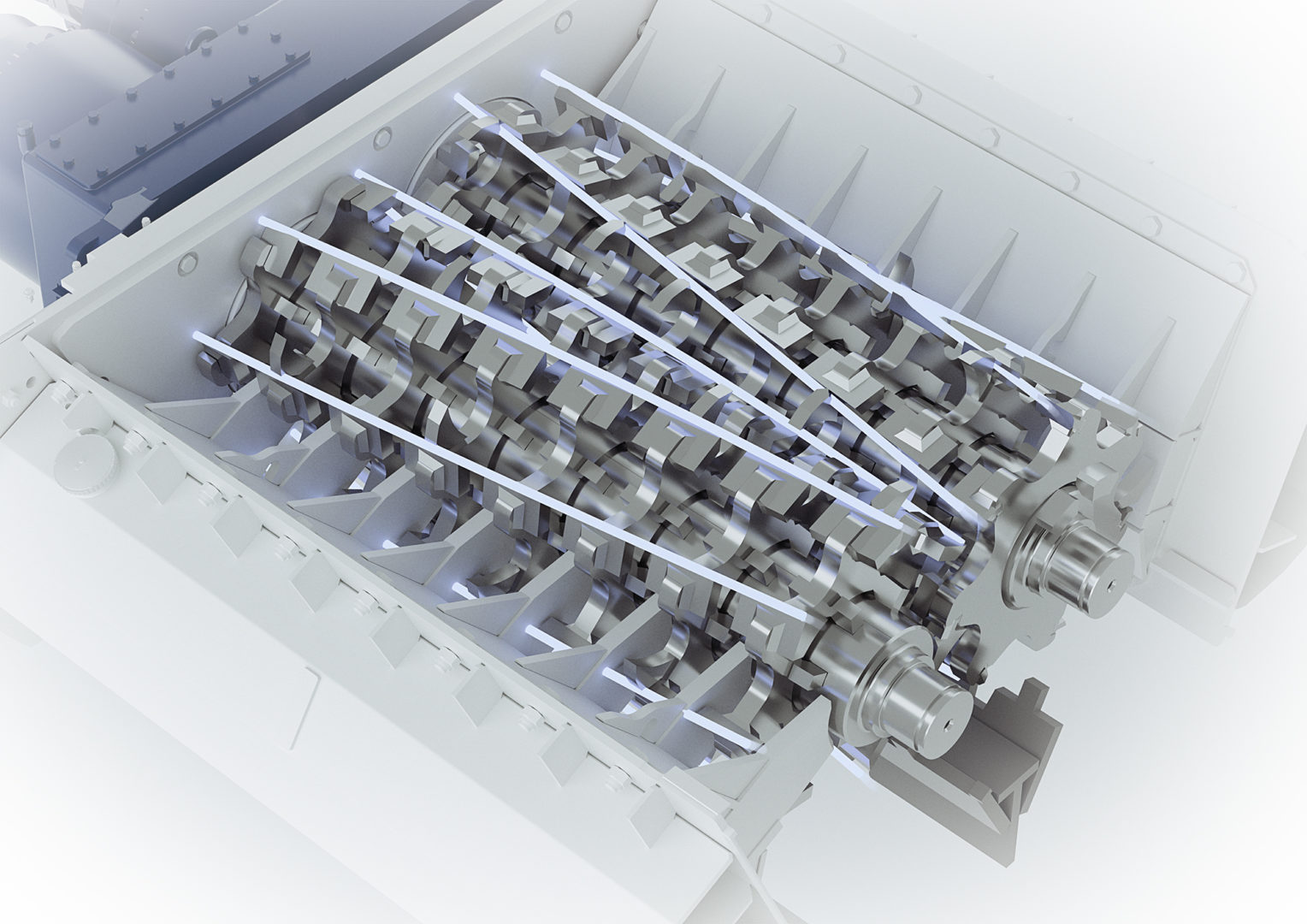
The easiest way to achieve smaller particles sizes would be to reduce the gap between the individual cutting tools. Conventional shaft pairs crush the material with rippers acting in parallel. If, in this case, the effective working range were extended, the amount of force required and thus the energy consumption would increase significantly. However, if the angle between the knives is changed, they act just like scissors, effectively applying force to a much smaller area. This massively increases the individual tools’ impact while maintaining the same energy consumption. Thanks to the ingenious arrangement of the knives, rippers and small blocks on Lindner’s SF cutting unit, the material is shredded up to four times in one pass. This results in smaller particles with a low percentage of fines. Since less force is needed, the shafts are subject to less stress, which in turn reduces maintenance and increases the cutting unit’s service life tremendously.
If we now look closely at the entire shaft, we see that the cutting edges are not aligned in parallel. Thanks to this arrangement the two shafts act just like two Archimedean screws rotating in opposite directions. What the ancient Greeks used to transport water over great heights with the help of gravity, positively affects the way the shredding unit pulls in the material. This aggressive intake increases the throughput enormously and also mixes the final fraction once again for an output that is as homogeneous as possible.
What needed to be proven
Past experiences show that, with just one single pass, Lindner’s shredders from the Urraco or Miura series equipped with these tools produce a standardised P100 particle size according to ISO 17225-1 with less than 4% fines during waste wood shredding. This standard basically describes in detail the percentages to be achieved as well as maximum specifications for the main fraction, oversized particles and fines (see Table 1). During the production of these standardised particles, depending on the configuration, Lindner’s extremely efficient twin-shaft shredders achieve 20 up to 120 metric tons per hour – an incredible result.
Class | main fraction | max. coase fraction | max. length | fine fraction |
P63 F05 | 60% < 63 mm | 10% > 100 mm | 350 mm | < 5% < 3,15 mm |
P100 F05 | 60% < 100 mm | 10% > 150 mm | 350 mm | < 5% < 3,15 mm |
P200 F05 | 60% < 200 mm | 10% > 250 mm | 400 mm | < 5% < 3,15 mm |
Typical particle sizes in Line with EN ISO 17225-1
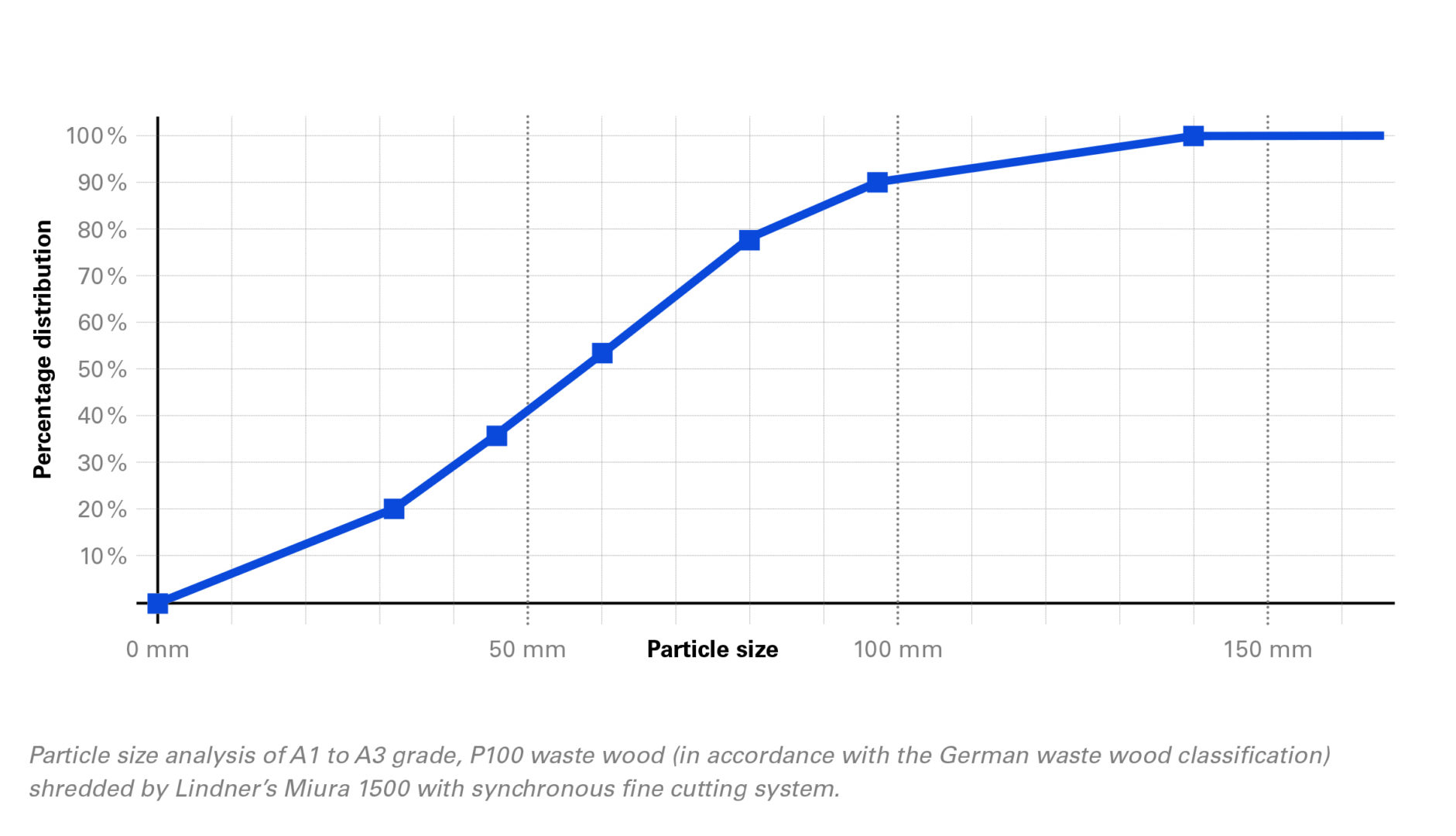
Particle size analysis of A1 to A3 grade, P100 waste wood (in accordance with the German waste wood classification) shredded by Lindner’s Miura 1500 with synchronous fine cutting system. Photo: Lindner Recyclingtech