Wet processing industry experts CDE have commissioned the companyâs first solution in Belgium for family-owned business De Bree Solutions as it upgrades its 20-year-old equipment range to boost process efficiency and respond to growing demand. Founded in the 1970s, the company, then known as Cleaning De Bree, established itself as a specialist sewage and waste collection service provider, offering septic tank emptying, cleaning and pumping amongst its range of services.
Having expanded its focus over the past five decades, De Bree Solutions, as it is known today, is active in industrial cleaning, green processing, soil cleaning, soil remediation, waste management, water purification and sewer renovation throughout Belgium, Netherlands and France.
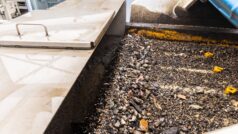
Its most significant shift occurred over two decades ago at the turn of millennium when, as a result of evolving environmental legislation, De Bree Solutions invested heavily in the latest recycling technologies of the day, establishing soil remediation and water purification facilities at its site in Maldegem and opening three new sites in Ostend, Eke and Schoondijke where valuable raw materials are, to this day, recovered from contaminated and inert waste streams.
Just as the company pivoted and adopted responsible waste processing practices over 20 years ago, the forward-thinking De Bree Solutions once again is investing in the latest waste processing technologies, engineered by industry experts CDE, as it enters a period of business growth and sustained demand for its product range.
“Now is the right moment for us to invest”
Yves Dupont, Managing Director at De Bree Solutions, says streamlining and making efficient an ageing plant setup at its Maldegem facility were key to supporting the company to grow sustainably and remain competitive. âWe have operated our current plant for over 20 years now, and in that time have invested in additional components designed to integrate with it. It has served us well over its lifetime, but now is the right moment for us to invest in an overhaul of the plant to address inefficiencies that have slowly developed over time.â
Eunan Kelly, Head of Business Development for North West Europe at CDE, says integration with the existing plant setup was essential for the project.
âAfter meeting with Yves and the team at De Bree Solutions we gained an in-depth understanding of what the business wanted to achieve: competitive advantage, reduced OPEX, cost-effective and efficient solutions. Top of the list was durable technologies that could integrate with the companyâs existing setup.
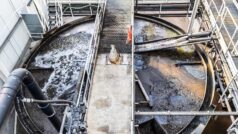
âEquipped with this knowledge, having also surveyed the site and the existing plant, we identified shortcomings in components, inefficient transfer points and a sand product that had the potential to achieve a higher specification; all areas of the plant that could be improved by CDEâs proven technology and processes.â
To meet growing demand for its product range, De Bree Solutions also sought to expand the processing capacity of its operation. With higher processing and production capacity, it was critical the solution developed was reliable, as Dupont explains.
âWith more material passing through the plant there is more need for downtime to accommodate maintenance and upkeep, and more potential for things to go wrong. Thatâs why, aside from the quality and quantity of product, the entire system had to be backed up by reliable technology which would reduce operational costs â producing savings we can pass on to our customers â and maximise plant uptime.â
CDE solution
The solution proposed by CDE included its AggMax, EvoWash and CFCU systems to process highly variable feed material including organic waste, contaminated soils containing metals, cyanide and oil; construction, demolition and excavation (CD&E) waste; and road sweepings.
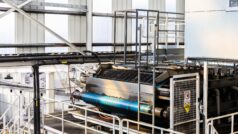
CDEâs market leading AggMax technology is engineered to operate in the toughest of conditions to maximise product yield from the most abrasive of feedstocks. Its versatile design incorporates five processes on a single and compact portable chassis, including pre-screening, scrubbing/attrition, sizing, contaminants removal and stockpiling.
The heavy-duty AggMax can process challenging CD&E waste material containing large quantities of organic and other inert physical contaminants into high-value materials suitable for a variety of applications in the construction industry.
Fine material is processed by CDEâs signature EvoWash technology. A compact, modular sand washing system, the EvoWash screens and separates the smaller sand and gravel fractions through an integrated high-frequency dewatering screen, sump and hydrocyclones which provide unrivalled control of silt cut points and eliminates the loss of quality fines with significant commercial value.
Incorporating CDEâs patented Infinity Screen technology, the EvoWash offers optimal dewatering results which enables materials processors to produce a range of high-quality sands that are market-ready straight from the belt.
CFCU technology allows for effective separation of two materials of differing relative densities. With a variable cut (separation) point, it offers greater control over sand classification providing complete flexibility for the production of various end products and the removal of lightweight contaminants from the fine material fraction.
Project pillars
The full solution was designed around the customerâs specific needs, Kelly explains. âReliability, plant maintenance, processing capacity, product specification and integration were the pillars of this project. Our solution eliminates the inefficiencies found in the original setup and integrates reliable and scalable technologies which are important for future growth.â
Where the original plant had two cyclones, it now only has one, which Kelly says is a less costly and more efficient way of working. An existing CFCU was also replaced, he adds.
âThe sand product wasnât of a high quality, but our tests showed it could be produced to a higher specification. It was the outdated technology that was letting it down.
âWe completely replaced the CFCU with ours to ensure consistent sand specification from a much more reliable system which requires less maintenance.â
400 tonnes per day
Integrating seamlessly with the existing plant setup, CDEâs tailored solution has almost doubled processing capacity at the Maldegem site.
âWeâre targeting 400 tonnes per day, in one production shift, of sand and stone which will of course vary due to the variable nature of the material we process, but the fact is that thanks to CDE we now have that capacity there which will help us keep up with growing demand,â Dupont explains.
Both the sand and aggregate fractions pass through the newly commissioned equipment which has increased capacity and improved output quality.
Stijn Declerck, Head of department GRC & WZI at De Bree Solutions, adds, âThere is indeed more and more demand and we want to run more material than ever before. The CDE plant has allowed us to keep up with the growing demand and grow our business.â
Washed sand processed by the CDE solution is being used for over 90% of concrete produced by De Bree Solutions for underground works, while the aggregate output is used for various applications, including concrete products, drainage and other construction-related applications.
Kelly says the project represents a major milestone for CDE as it continues to grow its presence on the ground in Europe.
âBelgium is a well-established market, so itâs a significant endorsement of our technology and process that De Bree Solutions selected us as their partner on the project, our first in the Belgian marketplace.
âWe believe that this project highlights how CDE can help improve existing operations with products from our extensive range. The right products and a great partnership have led to this being a very successful project for all involved.â